WHERE ACME'S QUALITY BEGINS
What is coke? Coke is the carbonaceous
sintered mass left after the destructive distillation of coal. To produce high
quality blast furnace coke, high quality coals must be used. High quality coals are
those coals that, when coked together, produce the highest "stability" and CSR
(coke strength after reactivity) to support the blast furnace burden and allow maximum
wind for maximum production.
Coal, however, is not a homogeneous commodity.
Coal is the carbon form of the fossilized remains of plant material that fell into
swamps which disappeared 60-300 million years ago. A lot of different things
happened to these geologically and geographically diverse deposits as they were laid down
and eventually coalified. If you add the different mining techniques, operations,
etc., to these natural variations, the coal delivered to the coke plant can have very
different characteristics. This is why we have a very tight quality control program.
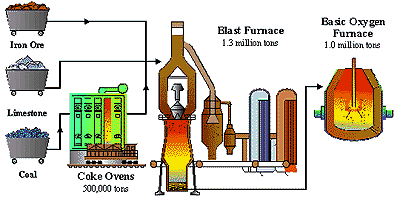
Coke being charged into "A" Furnace
Coke is produced by heating metallurgical coal
in the absence of air in a coke oven. Once the coal is transformed into coke it is
charged into a blast furnace which creates a chemical reaction to help convert iron ore
into pure liquid iron. This Chicago facility annually produces 500,000 tons of coke.
This plant stands as one of the world's cleanest, low cost producers of high quality coke
and coke by-products. In addition to steelmaking, coke is also used in the secondary
smelting and the sugar beet industry.
COKE OVEN CAPACITY AT ACME
The Chicago Coke Plant operates two 50 oven
double divided Wilputte underjet batteries. These batteries were constructed in 1956-57
and were through-wall repaired in 1978-79, replacing all 102 heating walls in the battery
complex. At that time a pushing emissions control system was added to control the
particulate matter from pushing operations.
Maximum coking capacity is 133 ovens per day
(18 hour gross coking time) at 18.4 tons wet coal charged into the 701 cu. ft. working
volume. The 2,450 tons of wet coal charged at maximum capacity are capable of producing
1,530 tons of coke per day.
COAL HANDLING AND PREPARATION
Coal is purchased on the spot market.
Acme Steel has no take or pay coal contracts. Quality control begins even before the
coal is shipped from the mine. Petrographic, chemical, and physical tests are
conducted on every coal before it is purchased from a prospective coal supplier.
Once a coal is found to be suitable, it is
shipped by truck to the Chicago Plant. The coal is dumped directly into stock hoppers or
ground hoppers. There are five main components in our coal blend: high volatile
coal, high volatile fluid coal, medium volatile coal, low volatile coal, and petroleum
coke. Each is reclaimed separately and fed into the coal preparation plant where
they are pulverized at 82% minus 1/8" and retained in one of the six mixer surge
bins. Since two coals can be blended at the reclaim hopper, the coal blend can
contain up to twelve different coals. The coals in the mixer surge bins are metered
out to a conveyor belt by mixer machines and are conveyed to the 2,500 ton coal bin at the
batteries at 500 tons per hour.
COKE PRODUCTION
Coal is drawn by gravity from the battery coal
bins into the charging car, also called the larry car, and is charged into a recently
pushed oven chamber. The oven is sealed and the coal is baked in the absence of air
for about 18 hours. After all the moisture and coal volatiles are distilled away, a
free standing mass of yellow-orange hot coke is ready to be pushed from the oven chamber.
Coal is charged into the ovens from the larry
car's three hoppers through three sewer-like man hole openings called charging holes in
the roof of every oven. A leveling bar on the pusher machine knocks the coal peaks
from under the charging holes and fills the valleys between the coal peaks. This
forms a rectangular coal mass in the oven. The coal volatiles are driven off as the
coal and resultant coke mass is heated to 1,900 degrees fahrenheit. To push coke
from the oven, four machines are needed. The pusher machine removes the pusher side
door and pushes the coke. The door machine removes the coke side door and, spotting
a coke guide (which looks like a cattle guide), channels the coke from the oven to the
quench car (which catches the hot coke). The fourth machine, the hood car, collects
the fumes from the hot coke. The quench car then takes the hot coke to the quenching
station where the coke is quenched with 7,000 gallons of water. The quenched coke is
then dumped on a coke wharf where it begins a 1½ mile journey by conveyor belt to a
screening station (where the fines are removed) and on to the blast furnace.
BY-PRODUCT RECOVERY
The coal volatiles baked away in the coking
process are collected as four major by-products: coke oven gas, coal tar, ammonium
sulfate, and light oil. Tar is the first by-product recovered in the train, by
condensing out as the gas is cooled. The condensed tars and coal moisture are
transported to the tar decanters, where the heavier tars are separated out and the water
is recycled to cool the gas in the collecting main and primary coolers. The gas then
passes through a massive compressor, called the exhauster, which pulls the gas from the
ovens and pushes it through the rest of the by-product train. Tar mists are removed
in electrostatic precipitators and pumped to the decanters. Ammonia is removed in
the absorber and processed into a liquid fertilizer. The secondary cooler cools the
gas to its final temperature and removes naphthalene, which is dissolved in the tar and
sold. The cleaned and cooled gas then passes to the LBA's, where benzene, toluene,
xylene, and higher aromatics are scrubbed from the gas and sold as light oil. The final
product is the cleaned coke oven gas, 38% of which is used to heat the ovens and make more
coke. The 62% surplus is sold to the boiler house and the blast furnace.
BENZENE NESHAP
In 1989, the U.S. EPA decreed that emissions
from the By-Products Division be reduced by 98%. The effective deadline of this
decree (called Benzene NESHAP), was September 15, 1991, at which time all vessels and
lines containing benzene had to be sealed from the atmosphere and gas blanketed.
Acme Steel met this requirement at a cost of nearly $10 million. All tar tanks, the
light oil tank, and two weak liquor tanks were replaced. All other vessels in the
plant were upgraded to meet these standards. A secondary cooler system was built to
replace the final cooler system and the ammonia stills were upgraded to handle the
additional liquor that was generated. The By-Products Division has been in
compliance with Benzene NESHAP and has operated reliably since startup.
GOVERNMENT AGENCIES
Along with producing a high quality, low cost
product, the Chicago Coke Plant makes every effort to achieve the high safety and
environmental goals set by Acme, and the Federal, State, and Local regulators to control
the ever persistent coke oven emissions. OSHA even has a special standard for coke
oven emissions. The success of these efforts can be measured by the lack of
significant fines from these agencies, and the fact that the Acme Chicago Coke Plant was
the first in the state of Illinois to receive its operating permit. In 1988, Acme's
Chicago Coke Plant was designated as a model plant by the Federal EPA. Acme's
Chicago Coke Plant won the "Max Eward Safety Award" in 1992. The American
Coke and Coal Chemical Institution presents this award each year to the Coke Plant in
North America with the best safety performance.
THE FUTURE
The growing scarcity and cost of low-residual
scrap makes the sale of hot metal/pig iron much more profitable, thus increasing the
demand for more and better quality coke.
The operating condition of the coke oven batteries is excellent. With proper, proven
operating practices, such as maintaining proper back pressure, cleaning doors, keeping the
refractory brick sealed and protected from the atmosphere, proper coal selection
--combined with new state-of-the-art technologies of refractory repair (such as ceramic
welding and the use of zero expansion brick), Acme believes that these batteries can last
almost indefinitely. The Clean Air Act Amendment has provided more challenges to all coke
plants in the United States, and Acme Chicago Coke Plant is able to meet all these
requirements.
Our success is attributed to our people.
The United Steel Workers Local #1657 and our strong dedicated management team continue to
work together for our common goal.