Very excited to share another great contribution from my friend Doug. Doug worked for Interlake/Acme from the mid 70s until the plant closed. At that time he was area manager for ovens. After more than two decades between the coke plant and Riverdale mill, Doug has seen it all and again he shared info that a very select group on planet earth are privy to.
You started your career in the coal handling department. Take me through the arrival of coal to the facility and what happens next.
The majority of coal processed at the plant arrived by rail. Coal was mainly shipped by CSX then transferred to the plant by the IHB (Indiana Harbor Belt). The tracks on the far side of the plant were NS (Norfolk Southern) mainline with Acme owning eight storage tracks. One of the storage tracks also had a spur that extended to the south property border and then to just west of the quench station.
Acme had no authorization nor the locomotive power to move coal from the main lines into the plant (we had two small transfer locomotives that could move four loads at a time up the hill on a good day). Chicago Short Line was under contract to load us up with cars from the main line.

On the west side of the property and behind the coal handling office there were 10 storage tracks with capacity for about 200 rail cars. CSL would set the “hill” (tracks running along the west side of the rotary dumper). A transfer locomotive would move two cars at a time from this track, south along the high line (elevated track) and switch to the track that ran thru the dumper. One car at a time was literally turned over – not quite 180 degrees – and the coal (most of the year) would gravity flow into three hoppers below the dumper. From there the coal was conveyed north as it elevated to a tower transfer point then conveyed back south and elevated to the two stock out hoppers. From the stock hoppers coal was loaded into huge Euclids and then laid out on stockpiles or brought round to the ground hoppers which fed conveyor belts to the pulverizer building.
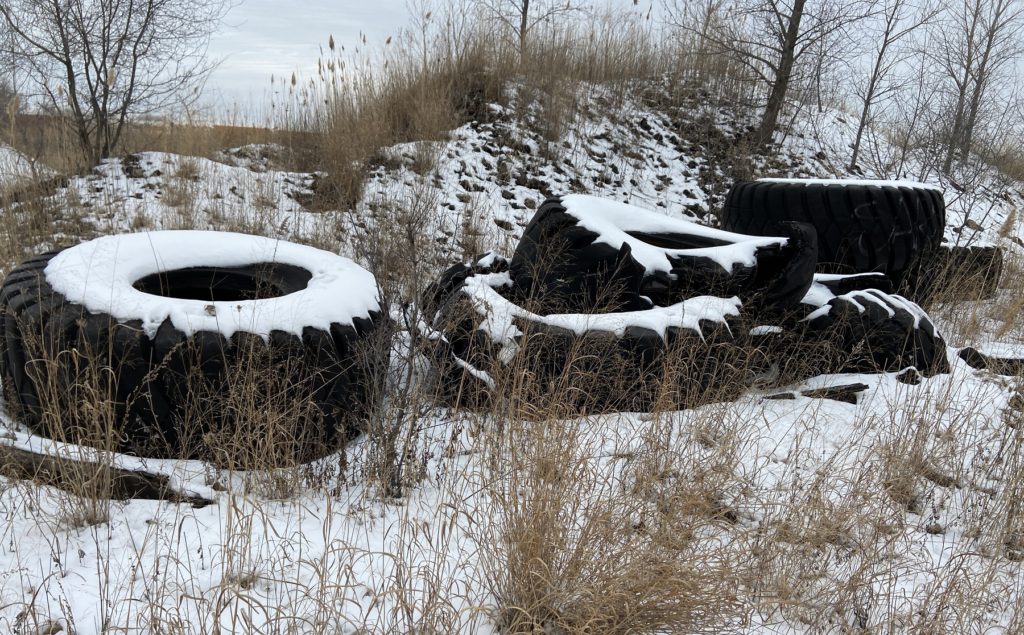
To make the best coke, particle size needs to be relatively equal so all coal was pulverized either through an ancient hammermill or a more modern Cage-Paktor (cage mill). The finer the better was good for coke. However fine coal runs like water when dry but not so much if moisture is high! And fine coal under the right conditions opens opportunities for explosive conditions and spontaneous combustion as well. Once again, always a balance.
What is the purpose of the giant rectangular pond next to the quench station?

Acme used to have an ancient diesel crane that would be used to dig coke breeze from the quench water sump. The sump was a settling basin to let the fines or the occasional larger pieces of coke that were washed from the quench car during the quench settle out with “clean” water flowing through screens to the make up sump. Inside the quench station on the east side there was a drain that connected to the sump by pipework running under ground. Water flowed thru pipework from the sump to pumps (basement of the quench station) where it was pumped up to a holding tank which used to be above the quench station. Occasionally pieces of coke would find their way thru the screens and pumps and plug the quench sprays in the station (there were six sprays in total). Quenching coke was a balance between adding enough water to put out the glowing red coke but not too much.
After being deposited on the wharf, coke would then be fed via conveyor through transfer points which directed coke to the blast furnace (across Torrence Ave., continuing across the Calumet River to the screening station at the Burley furnace plant) or moved to a stacker conveyor system at the coke plant if the furnace wasn’t taking coke.
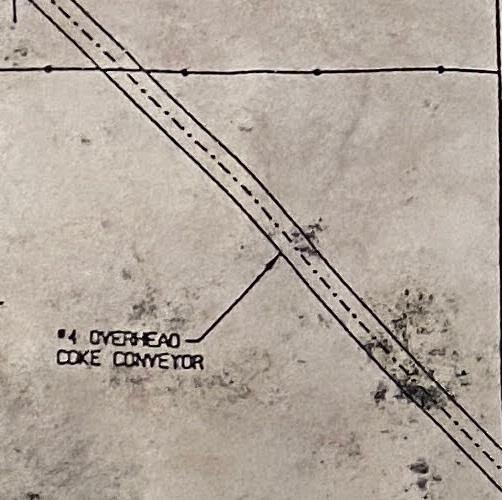
I’ve seen references before that call this conveyor “#4”. Where are 1, 2 and 3?

The #1 belt ran underground from the coke wharf to a transfer chute (also underground) just east of the center of the coal bunker structure. A flop gate in the transfer chute could be thrown to direct coke to the #4 belt and the blast furnace. Or to the #3 belt which fed to a stacker belt for stocking coke. There was also a reclaim hopper that via a chute could feed coke directly onto #4 belt so we could reclaim stock when needed. There was no #2 belt. That was eliminated before I started by modifying #1 to directly feed the transfer chute.
I really enjoyed the paper that Dr. Lin and Jack Garzella wrote for the Steelmaking conference in 1986. Coal blending seems like a pretty precise science.
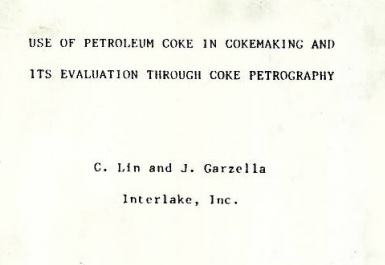
He pioneered the use of “petcoke” (residue of petroleum refining process) as a means of adding cheap carbon units to the coal blend. He was a true genius in his field. Because all met (metallurgical) coals have different properties and react differently when heated there is no ideal coal for coking. The key is to identify the properties and create blends of the different coals available to create the perfect coal blend – that was was the sole responsibility of Dr. Lin.
What is the story with the giant ‘Q’ sign that used to sit at the end of the driveway past the gate house?
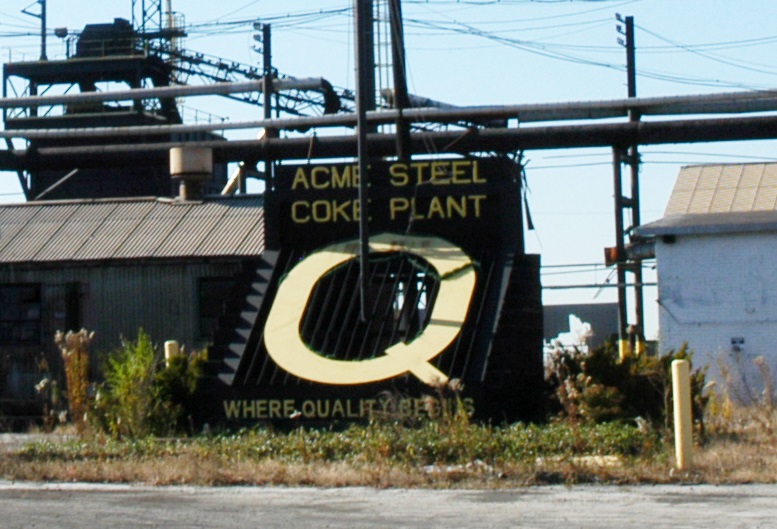
The large gaudy structure with the Q was created to represent our efforts at certifying for QS9000. It was a quality program which certified our production methods. It was important to be certified to gain government contracts for our finished steel.
What was the plant doing with such massive deliveries of propane?

Liquid propane? In a plant that is producing gas? Yep. We contracted with a company called Hotwork International and adapted their process for drying refractory brick repair into a method for blowing hot air into buildings and enclosed areas to facilitate material movement in the winter. Basically huge torpedo type heaters with all the ductwork into the required areas. Very expensive but it did make it possible to facilitate coal handling even during the most severe winters.
What can you tell me about the circular charts I’ve been spotting in the BP plant and also now in the coal bunker?
Your trove of circular charts were very important tools, especially in the by products plant. The were measuring either internal pressures, temperatures or both at every vessel, gas main and gas collector main – 24 hours a day. The gas was generated in the oven, sucked off by a huge gas pump called an exhauster and then pushed thru primary cooling towers, ammonium sulfate plant, through final coolers, into the light oil recovery stills and back to the ovens – hopefully clean enough to burn properly. It was a total chemical process in action. The only way to know if it was running right was the charts. Easy to find operation problems before they got out of hand if you knew what to look for!
4 replies on “Q&A with Doug”
This is great! Hope you do more Doug interviews in the future!
we FaceTimed for about 45 minutes on Saturday while I was in the plant – we will definitely continue to collaborate. Glad you enjoyed!
That must have really got him feeling reminiscent!
it did. part of that Q&A i actually took from our text message conversation of which there are many. he really shared some awesome anecdotes about specific people (most not fit for publication). I’m really lucky I located him!